Um Keramik herzustellen, benötigt man sogenannte Arbeitsformen. Arbeitsformen sind das Negativ des Formlings. Diese werden aus Modellen hergestellt. Es gibt Drehformen und Gießformen. Bei den Gießformen unterscheidet man zwischen Hohlguss- und Vollgussformen.
Modelleinrichtungen aus Gips haben eine geringe Lebensdauer, da das wiederholte Abgießen zum frühzeitigen Aufrauhen der Oberfläche führt (besonders bei Formen mit Relief). Daher verwendet man auch Modelleinrichtungen aus Harz, Silikonkautschuk und Polyurethan. Aus den Modelleinrichtungen erfolgt in großer Anzahl die Herstellung von Arbeitsformen.
Nichts ist von Dauer: Bei Gipsformen sind ca. 150 Ausformungen möglich, bevor diese ausgetauscht werden müssen. Bei Polyurethanformen erreicht man zwischen 5000 und 8000 Abformungen.
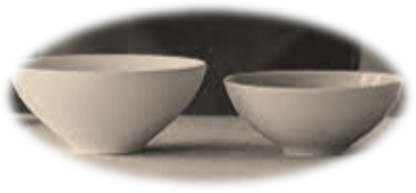
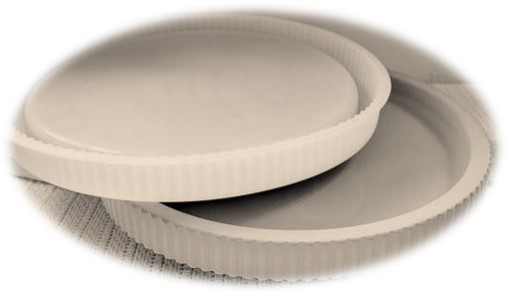
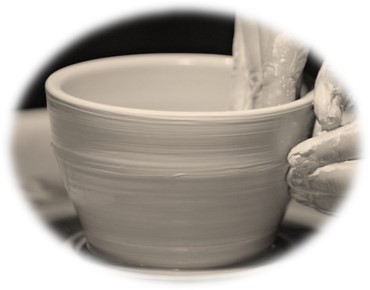
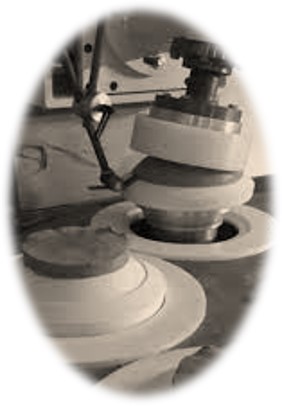
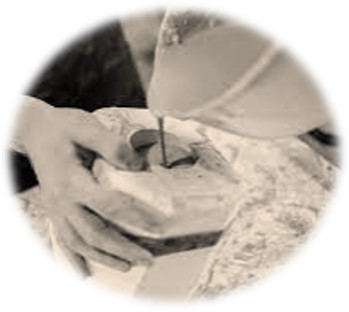
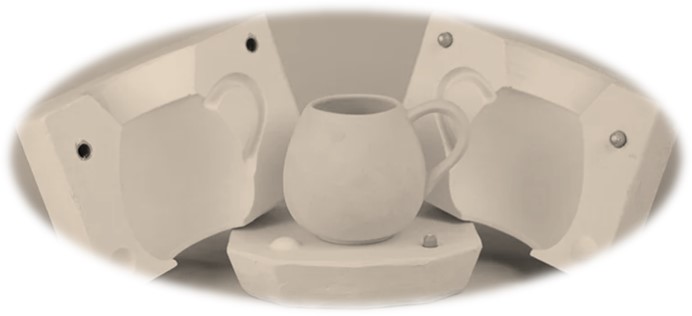
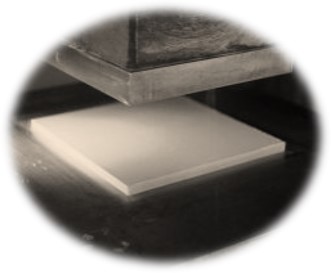
Ihr könnt in unserer Schauproduktion viele verschiedene Gipsformen aus mehreren Teilen anschauen und selbst zusammensetzen.
Schwindungsgröße
Und ohne Mathe geht selbst bei uns nichts….
Bedingt durch das Trocknen und Brennen verkleinern keramische Gegenstände ihr Volumen – sie Schwinden. Daher müssen die Modelle immer größer als das fertige Produkt sein.
Die Schwindungsgröße wird wie folgt berechnet:
Modellgröße (M) – Schwindung (S) 15 % = Glattbrandgröße (G)
Formgebungsverfahren
Es gibt drei Formgebungsverfahren:
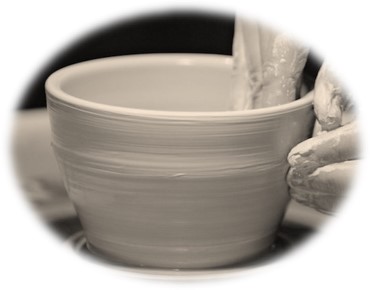
Drehen

Gießen
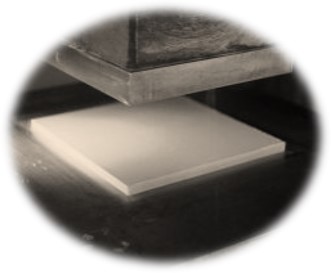
Pressen
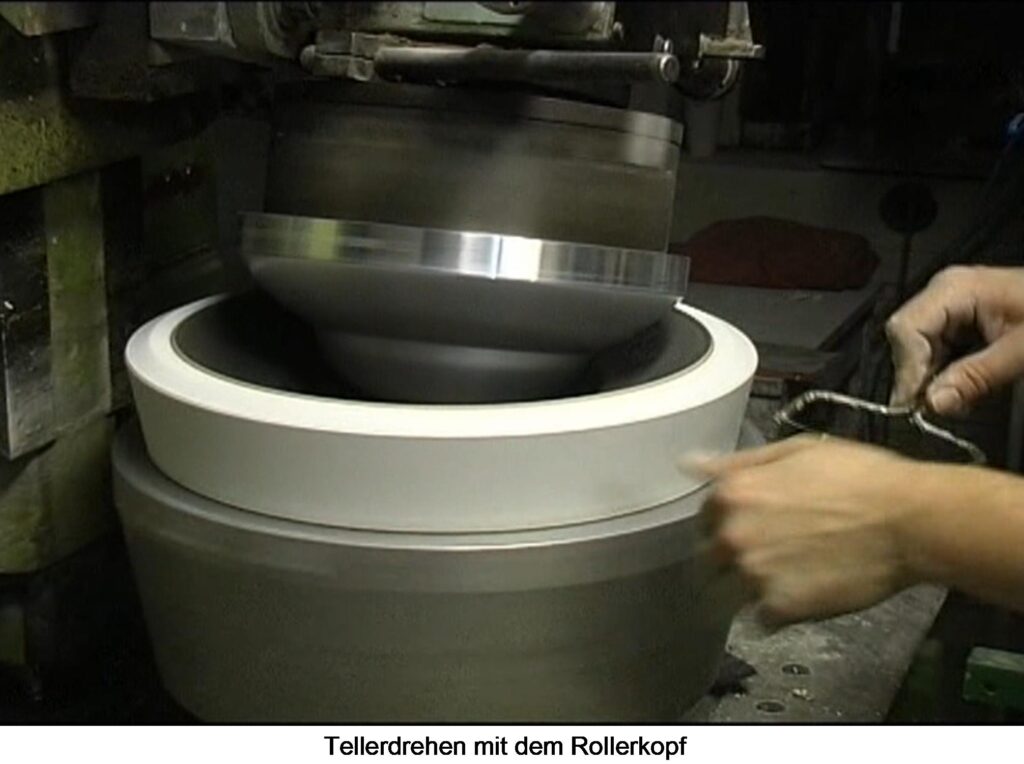
Die einfachste mechanische Vorrichtung zum Drehen ist die sogenannte Drehspindel, welche ein Nachfolger der Töpferscheibe ist und für das Drehen rotationssymmetrischer Formlinge verwendet wird.
Die Arbeitsformen sind i.d.R. aus einem Stück gearbeitet, wodurch beim Ausformen am Rohling meist keine Nähte entstehen, die durch „Putzen“ beseitigt werden müssen
Wichtig ist die Einhaltung der Drehzahl: Kleiner Formling – große Drehzahl
Großer Formlimg – kleine Drehzahl.
In der Feinkeramikindustrie nennt man moderne Formgebungsmaschinen zum Drehen ROLLER.
Dabei wird eine Leerform aus dem Trockner entnommen und in den Aufnahmering am Drehtisch gesetzt. Bei Hohlgeschirr, wie z.B. Tassen, wird die benötigte Masse in die Form eingegeben. Durch Drehung des Tisches gelangt die Form unter den Rollerkopf. Durch ein Vakuum sitzt die Form fest in der Formenaufnahme. Das Absaugen der Luft geschieht durch das innere einer Hohlspindel. Durch ein Absenken des heißen Rollerkopfes wird der Rohling der Form entsprechend ausgeformt.
Heute dreht man mit sogenannten Rollerkopftaktstraßen große Mengen in kurzer Zeit.

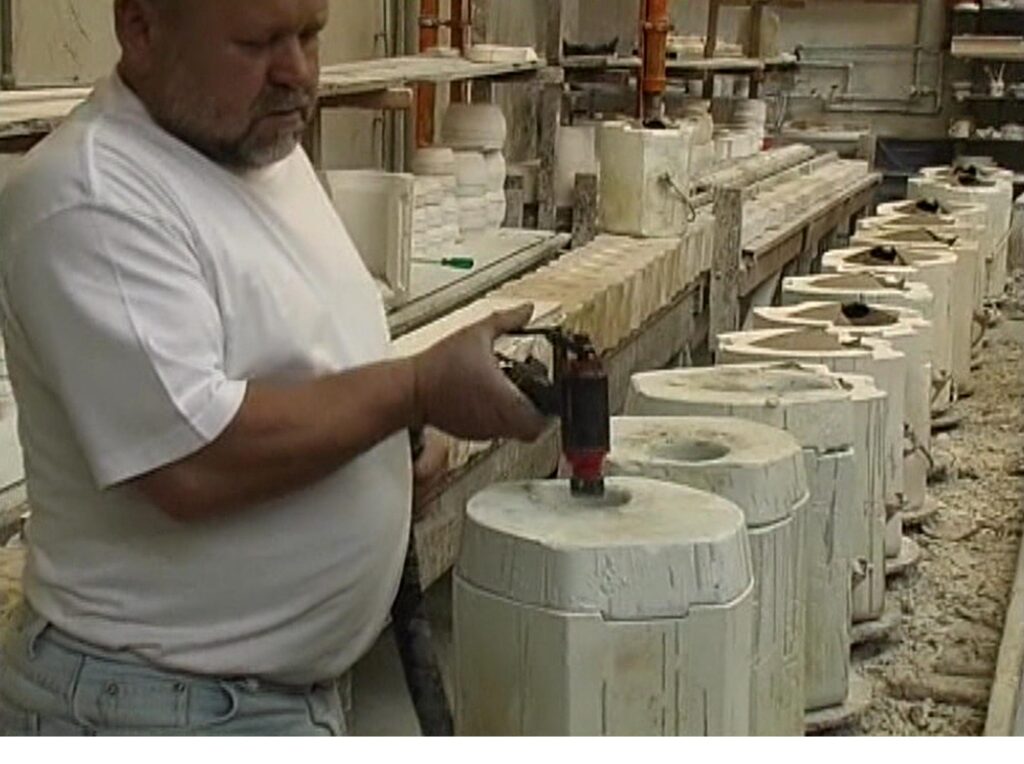
Das Gießen erfordert beim manuellen Arbeiten neben einer relativ großen Produktionsfläche viel Zeit. Da die Arbeitsproduktivität bei diesem Verfahren niedrig ist, wird der Formgebung durch Drehen oder Pressen meistens der Vorzug gegeben, wenn es technologisch möglich ist.
Gegossen werden in der Regel asymmetrische Formlinge (Kannen mit Henkel, Formlinge mit starken Reliefs). Für die Herstellung sanitärkeramischer Erzeugnisse ist es das vorherrschende Verfahren.
Die Gießmasse nennt man SCHLICKER.
Das Gießverfahren wurde erstmals um 1780 in Belgien angewendet und gelangte erst um die Jahrhundertwende zu größerer Verbreitung.
Die schwere körperliche Arbeit und die relativ niedrige Arbeitsproduktivität verlangte nachdrücklich mechanische Gießanlagen wie z.B. Gießbänder, Gießelevatoren, Gießmaschinen. Durch Gießmaschinen wurde die körperliche Arbeit erleichtert, führte jedoch auch zu größerer Lärmbelastung.